Talk about inflation seems to be happening more and more these days as we see news articles reporting anywhere from 2% to 5.4% annualized gains. These headlines, however, don’t tell the whole story as they’re often used as indicators for either the economy as a whole or more consumer focused aspects of the economy. Utility and city managers need different information to help prepare for potential cost increases in their budgets. These costs can be bucketed into two categories – operations and maintenance, and capital costs
Operations and maintenance costs will be largely driven by either electric prices, depending on how energy intensive your treatment and pumping is, or personnel. We will take a deeper dive into those cost increases at a later point in time, but it is prudent to prepare for at least those headline numbers.
While energy and labor drive operating costs, building materials and labor will drive construction costs. Since these building materials are a key component of capital construction, the notable increases in lumber and steel prices are a cause for concern. Thankfully, the bulk of some of the most notable increases have not persisted, and prices of lumber, for example, have come down from their peaks.
It’s clear that everyone should be planning for cost increases, but given the uncertainty and the volatility the biggest question is how much? To help answer this, let’s review recent information from ENR’s cost indexes. ENR has two key indexes to track cost inflation. One is the Building Cost Index (BCI) that incorporates local union wages for skilled trades such as bricklayers, carpenters, etc., along with the cost of building materials. The other is the Construction Cost Index (CCI) that uses general laborer wages along with the cost of building materials. ENR compiles this information across 20 cities nationally, providing a perspective of regional trends along with a national composite.
The table below shows the 12-month change in BCI and CCI for two cities, Denver and Minneapolis, in October 2021. While this is only a snapshot in time, these values are considerably higher than anything seen in recent history. While they will continue to change and the 12-month change gradually reverts to the mean overall, costs are likely going to be higher on projects than when they were estimated this time last year. How much higher will depend on your project, the specific skilled labor requirements, the availability of specialized building materials as we continue to see supply chain issues, and the timing of when the project was bid. A conservative rule of thumb would be building in an additional 15% contingency into project planning.
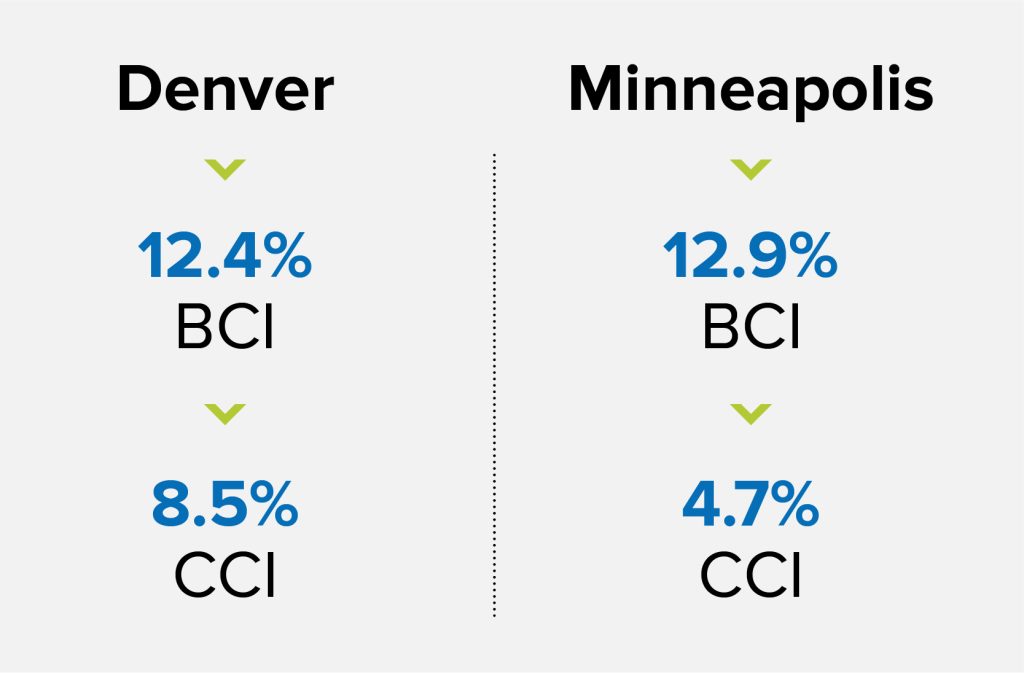
While evaluating overall project costs, there are some additional items to consider that can help prepare for these higher prices. Specifically, Nexus recommends:
- Evaluate your infrastructure funding policy – does your utility carry all the costs? If the utility is cost sharing these projects with residents, make sure to communicate changes to costs with the affected stakeholders so they are better prepared to cover their share.
- Check your project prioritization – if costs increase, you may have to delay some of the projects to stretch your limited funds. Making sure your projects are prioritized now can streamline that process if it becomes necessary.
- Rethink the overall design – sometimes creative engineering solutions can help to identify lower cost approaches or even phases that may be better added later, helping to control costs up front as material prices increase.
If you have questions about preparing for cost increases or my recommendations, feel free to contact [email protected].